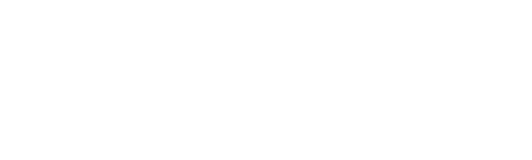
DESCRIPTION
FOAMGLAS® PC® 58 is a two-component modified bitumen based cold adhesive without solvents.
It is used as an adhesive and as a coating. After complete drying, the adhesive is flexible and resistant to numerous salty solutions, water and weak acids. PC® 58 is used to apply FOAMGLAS® slabs to horizontal concrete and porous concrete surfaces. It is also used to coat the surface of FOAMGLAS® slabs; prior to the application of bitumen based torch-on or self-adhesive membranes.
APPLICATION
Pre-treatment of the subsurface
The substrate must be clean, dry and free from grease, dust, oil and humidity. A primer coat of PC® EM (diluted 1 to 10) is required on the substrate. Alternatively use a diluted liquid component of the PC® 58 (diluting rate 1 vol. part of the liquid component, which must be diluted with 10 parts of water).
Preparing the glue or contact layer
To avoid waste and to maintain the desired properties, certain basic rules should be observed:
– Setting and pot time are influenced by the temperature (typically approx. 15-20 mins).
– Application temperature + 5 °C to + 35 °C.
– Have water and solvent ready to clean the tools.
– Mix the whole quantity of adhesive in the PC® 58 container
– The powder component must be continuously added in the stated ratio to the liquid component and carefully stirred while using an electric or pneumatic mixer (750 W, idle run 500 to 1000 r/min) until a homogenous and lump-free mixture is achieved.
– PC® 58 must be poured out of the container onto the substrate and spread with a rubber squeegee over the width of the FOAMGLAS® materials being laid, approx 600mm.
– Dip the edges of the FOAMGLAS® slabs in PC® 58 to ensure the edges are fully coated.
– Lay the FOAMGLAS® slab in the PC® 58 adhesive at a distance of approx. 10 cm from the already installed slabs and push diagonally into the open corner so that the joints are completely filled with adhesive and butted up tightly.
– To use as a surface coating; pour the mixed PC® 58 on the installed FOAMGLAS® slabs and spread over the surface with a rubber scraper. Note: Curing time at 20 °C and 65 % relative humidity is approx 90 min, after which the PC® 58 will shed water.
– After complete drying of the surface coating, a bitumen membrane waterproofing can be torched on. Make sure that the flame uses the bitumen mass of the membrane for adhering. A direct flaming on the coating has to be avoided. Alternatively a self-adhesive, cold applied, or hot melt membrane may be applied with a suitable and recommended primer.
Cleaning the tools
If the adhesive is still fresh, clean with water; if it is already dry, use white spirit.
Product Safety Notice
All material safety data sheets (MSDS) are available. They aim to ensure a safe handling of the product and correct disposal by the customer.
Description | Value |
Colour | Black / brown |
Type | Two-component adhesive |
Consistency | Pasty |
Application temperature (air + subsurface) | + 5 °C to + 35 °C |
Surface drying time | Approx. 3 hours |
Depth drying time | 1 to 3 days |
Reaction to fire (EN 13501-1) | E |
Downloads |
---|
PDS |
SDS Comp A |
SDS Comp B |
Click on the items above to view or download information. To download multiple items as a zip file click + or simply click the check box to add to a collection.
Please Login before adding files to a collection.